
Achieving Agility in Satellite Manufacturing
Aerospacelab is using an industry-leading approach to vertical integration that is reducing the time and cost of manufacturing satellites. By using standardized parts to build customized satellites, the company's Versatile Satellite platforms can meet the high demand for LEO satellites.August 22nd, 2024Aerospacelab is using an industry-leading approach to vertical integration that is reducing the time and cost of manufacturing satellites. By using standardized parts to build customized satellites, the company's Versatile Satellite platforms can meet the high demand for LEO satellites As the world becomes more interconnected and reliant on space-based technologies, the importance of expanding satellite platforms is set to surge for both commercial and defense applications. For commercial enterprises, a greater number of satellites facilitate enhanced global communications, more precise navigation systems, and improved data collection which drives innovation and economic growth. In the realm of defense, an increased satellite presence strengthens national security by providing superior surveillance, real-time intelligence, and robust communication networks.
The growing complexity of global challenges and technological advancements underscore the critical need for a more expansive and resilient satellite infrastructure, which requires a readily available and diversified source of satellite manufacturers and services.
This need of end-to-end satellite solutions and services for both government and commercial customers around the word drove Aerospacelab’s model of providing not only satellite platforms, but critical subsystems, mission payloads and turnkey satellite solutions for a variety of customers with diverse missions. Understanding the need for scalability and agility, the company built its overall operations with a focus of streamlining customer experience.
“Our goal is to meet the high-quality standards of exquisite satellite constellations with the affordability and agility of new space,” said Benoit Deper, founder and CEO of Aerospacelab. “Our approach to doing is becoming one of the most vertically integrated satellite manufacturers on the market, and partnering with customers from design, build, launch and post-launch services once in orbit. The less a customer has to connect multiple dots, the quicker we can field capability”
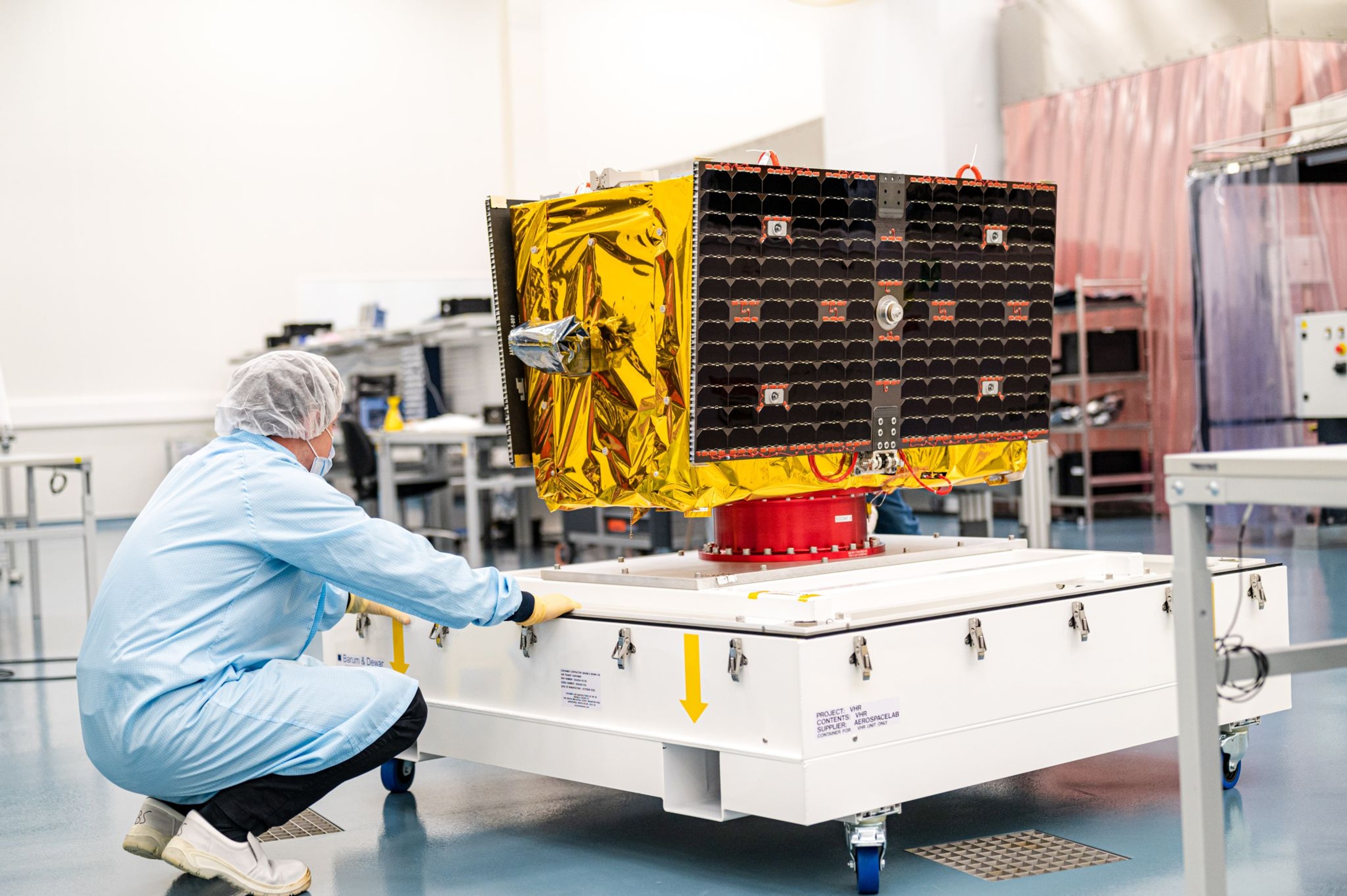
Vertical Integration: Key to Agility and Affordability
Aerospacelab is one of the most vertically integrated satellite manufacturers in the industry. Currently 90 percent of Aerospacelab’s satellite subsystems are designed and produced in-house. The company expects this figure to increase to 99 percent by 2026. Vertical integration reduces satellite manufacturing costs by eightfold, according to the company. In-house manufacturing also ensures high-quality standards, full transparency, and schedule control, while on-time delivery keeps mission costs and payroll costs under control.
“We are committed to our vertical integration strategy because it not only streamlines the customer experience, but gives us the ability to continually improve the product, become more agile in implementing those changes and reduce cost and timeline to delivery, ” said Deper.
With the aim of increasing transparency, the biggest benefit of vertical integrating is reducing the burden on having to navigate a turbulent supply chain landscape. Delays driven by component shortages or supplier delays can set a program back by months.
The use of commercial-off-the-shelf parts up qualified for use in space missions helps not only reduce the risks inherent in supply chains, but also reduces the overall costs creating more value for end customers. Affordability is also achieved with a goal of not over-engineering or paying for capabilities a customer does not need, but instead, looking for opportunities to simplify the product to make it easier to manufacture and accelerating the program schedule.
“If you need ten subsystems and you buy them from ten different vendors you end up with 10 different boxes with cables between them. Most of these boxes have computer hardware. You could reduce the number of FPGAs [field programmable gate arrays] or CPUs [central processing units] by converting the software functions on a smaller amount of chip, “ explains Deper. “It is super difficult to do if you are buying those boxes, because nobody is willing to open the design and share the IP in a joint tradeoff to rationalize the architecture. The goal is to be able to reshape the satellite architecture and lay the IP out on the table and say ‘How do we combine this in the most efficient way?’”.

Versatile Satellite Platforms
The approach to vertical integration also creates more opportunities for standardization in creating satellite platforms. Understanding that customers have unique needs for their satellite platforms depending on their mission and payload, Aerospacelab is aiming to balance customization with standardization that allows them to rapidly turn satellites to meet the demand of both commercial and government customers.
Aerospacelab designed the Versatile-Satellite Platform (VSP) family, a flight-proven satellite platform ready to support a variety of LEO missions. With a standardized modular core design, the VSP is quickly adapted for a wide range of payloads, including optical imagery, radio frequency detection instruments, telecom payloads, space domain awareness and missile tracking.
The Aerospacelab Versatile Platform line is growing to address the future needs of higher power telecom payloads. The current VSP family includes the VSP 50, VSP150, VSP 300, and very soon VSP450+. The foundation of these platforms comes from our in-house subsystems which are the standard building blocks that deliver more performance for the larger payloads. Aerospacelab has optimized the platforms for size, weight and power (SWaP) based on industry standard launch vehicle interfaces. As an example, the VSP 150 is optimized for a 1/2 plate on the SpaceX Rideshare mission profile. Aerospacelab is also well positioned to offer tailored solutions for larger, non-standard payloads, relying on the heritage of its VSP platform portfolio.
Designed to be compatible with serial manufacturing, the VSP product line is ideal for in-orbit demonstration missions as well as satellite constellations. The VSP is suited to the needs of both optical and communication payloads. Stability, pointing accuracy, availability and maneuverability have all been considered in the architecture and design.
Aerospacelab successfully launched six VSP-150 platforms; three hosting Optical Payloads for Earth Observation missions and 3 hosting RF Sensing payloads. Today, each satellite is operating nominally and performs targeted communication and data acquisition across the Earth’s surface by leveraging the VSP’s high pointing accuracy, platform stability and maneuverability.
The first VSP-150 launched by Aerospacelab on SpaceX Transporter 8, Grégoire, carried an inhouse developed Free-Space Optical Communication (FSOC) terminal to transmit data to the ground via an optical link. The next launch on SpaceX Transporter 9, SPIP carried a Multi-Spectral Imaging payload. SPIP captures multispectral images, useful for characterizing natural environments for agricultural planning, climate change, infrastructure and land-use monitoring.
The recently launched set of 4 VSP-150’s on SpaceX Transporter 10 become the new additions to the Aerospacelab fleet. These satellites include a Very High Resolution Satellite, Rose, and a trio of satellites (Riri, Fifi, and LouLou), Rose takes very-high resolution images that can be used for emergency response, asset and infrastructure monitoring, and urban planning.
Riri, Fifi, and LouLou carried Radio Frequency Sensing (RFS) payloads. This trio’s mission is to fly in formation and identify and characterize radio frequency emissions for use-cases including asset tracking, supply chain monitoring, geo-location and emergency search and rescue operations as well as identifying any jamming devices.
The demand for LEO satellites across government and commercial sectors requires the aid of commercial companies coming in with affordable and readily available supply of satellite platforms. The government customer seeks accelerated deliveries for security and the commercial customers are looking to accelerate their go to market objectives.
“Aerospacelab has made remarkable progress in six years, but thinking about what the team can do in the next six is what gets us all excited and motivated.” said Deper. “The needs are there, so while we have created the ready-now solutions our customers need today, I believe deploying the new variants of the higher power VSP, with different payloads in the future will continue to push innovation, agility and realize the vision for multi-orbit architectures. The goal in the end is the same—to use satellite technology to enable connectivity, improve security and quality of life on Earth.”