
FEEP: Field Emission Electric Propulsion
Changing perspectives on electric propulsion.July 28th, 2024Changing Perspective on Electric Propulsion
With more than 200 propulsion systems in space and an accumulated on-orbit time of over 400 years Field Emission Electric Propulsion (FEEP) technology has become one of the most mature and robust space propulsion technologies in the industry. ENPULSION’s FEEP propulsion systems have been used for a wide range of different applications and use cases. The company has used its extensive heritage and experience gained to develop and improve a new generation of propulsion systems.
In parallel, ENPULSION has matured and expanded its production capabilities, and operates an active serial production, as well as an ISO-certified quality management system with the goal to further advance its position as the most dependable tier-1 in-space mobility solutions provider in the market.
Since the first flight of a Field Emission Electric Propulsion (FEEP) thruster in 2018, more than 200 of ENPULSION’s propulsion systems have been launched. These propulsion systems are based on passively fed, indium based liquid metal FEEP technology that was developed at AIT and later FOTEC, and in which thrust is generated through electrostatic acceleration of ions extracted from a liquid propellant.

FEEP Technology Principles
FEEP propulsion generates thrust by electrostatic acceleration of metal ions. Ionization is achieved from a liquid propellant applying high electrostatic fields between the metal propellant and an extractor electrode. In the ENPULSION FEEP systems, the metal indium, which is solid at room temperature during assembly, integration, and testing as well as during launch, is liquified once in space and used as metal propellant. This brings many advantages to the technology. FEEP has the highest total impulse per volume and per wet mass compared to other electric propulsion technologies, due to the very high density of indium, when compared to propellants like argon, krypton, xenon, or iodine – and it makes FEEP systems very compact.
Since propellant liquification is only done once in space and for ground vacuum testing, the FEEP system is fully solid and inert during ground handling, integration, and launch. Emitted propellant is replaced in a fully passive manner by capillary forces which maintain propellant supply from the propellant reservoir up to the emitter tips, relying solely on surface tension of the propellant itself. FEEP thrusters therefore do not require any external forces like pressurization or pumps. Even at end of mission, the system does not need to be passified, as it is self passivating.
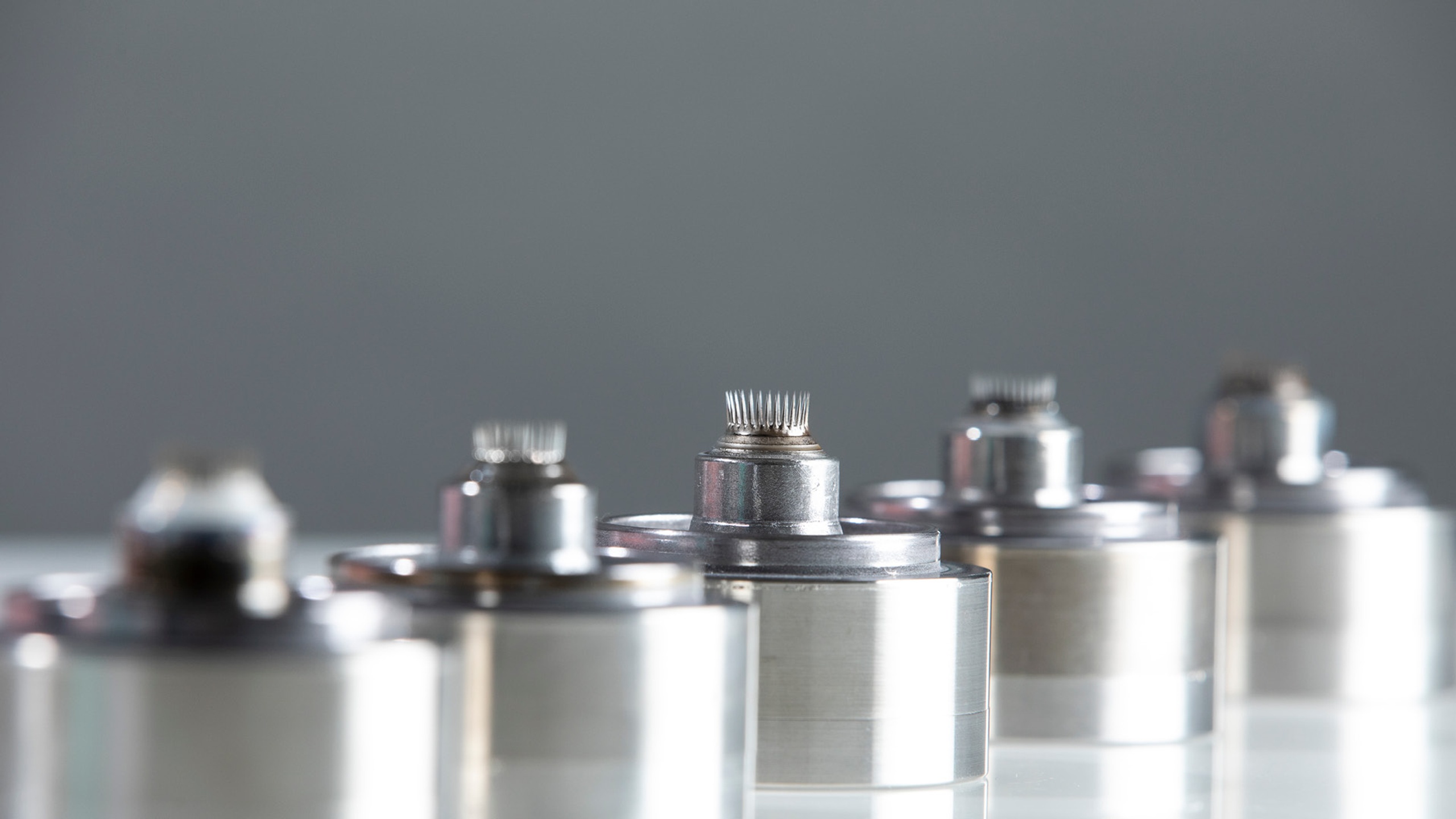
For assembly, integration, testing, and launch this comes with additional advantages. FEEP propulsion systems are fully integrated and contain the tank as well as propellant. Systems are shipped full and no additional filling operations at the satellite manufacturers facilities or launch facilities are required. No part of the propulsion system is pressurized, and since the indium propellant is non-toxic, non-reactive and non-radioactive, there is no need for additional safety requirements, which leads to tremendous cost and time-savings for satellite manufacturers.
FEEP Advantages
- No pressurized components
- No additional safety requirements
- No filling operations
- No hazardous, reactive or radioactive materials
- No additional launch requirements
A New Generation of FEEP Products
Based on the significant heritage in testing, production and on orbit gained on the heritage ENPULSION NANO thruster that was used in the first in orbit verification in 2018, several successor propulsion systems – the R³ systems – have been developed.
The ENPULSION NANO R³ as an improved version of the NANO featuring among other improvements higher radiation tolerant electronics and improved mechanical design to simplify integration, the ENPULSION NANO AR³ that introduces thrust vector control without movable parts, and the increased power ENPULSION MICRO R³ which expands thrust range beyond 1mN.
All of these new propulsion systems have successfully achieved flight heritage. Over 200 FEEP propulsion systems have been launched. While the majority of FEEP systems on orbit continues to comprise of heritage NANO propulsion systems that remain at high launch cadence, the updated flight statistics also reflects the successful introduction of the successor products NANO R³/AR³ and MICRO R³ reflected in increased numbers being deployed. To date, multiple individual propulsion systems, including R³ systems, have surpassed accumulated firing times beyond 1,000 hours of operations.

FEEP Use Cases
FEEP technology has been used in space for a wide range of use cases and applications and offers some unique advantages to satellite manufacturers.
ENPULSION FEEP propulsion systems have successfully been used for:
- Constellation deployment
- Station keeping
- Orbit raising
- Orbit phasing and Ground Track Improvement
- Formation Flight
- Collision avoidance
- Drag Compensation
- Small GEO Demo Missions
- Commercial BIU Missions
- Several units in space are foreseen to perform de-orbit maneuvers once the first operational missions are over

Advantages of Indium
Propulsion systems using indium are very compact due to its high density — compared to Hall-Effect thrusters or other systems using xenon, krypton or iodine as propellants.
FEEP Thrusters are shipped full – and no additional filling operations are required at the satellite manufacturer’s facilities or launch facilities.
It is safe — Indium is non-toxic and easier to handle than other propellants. It is stored unpressurized and, unlike high pressure tanks, does not need special authorizations (launch waivers) to be launched as secondary payloads, and is RoHS and REACH compliant.
It is inexpensive and readily available — Indium is currently a by-product of zinc refining and benefits from industrial scale production.

Heritage and Reliability
Industrial Capabilities, Active Serial Production, and Dependable Lead Times
With the experience gained, ENPULSION has tripled the size of its production facilities in 2024 and greatly increased its production capabilities. The company has an active serial production currently shipping up to five propulsion systems per week, which allows it to offer very short and dependable lead times.
ENPULSION has implemented an ISO-certified lean manufacturing process, and its meticulous planning and execution occur at every stage of the manufacturing process, spanning from assembly and integration to acceptance testing and continuous improvement to ensure the best possible product outcome. The company’s ISO class 6 clean room environment provides the optimal conditions for product assembly and integration. All products undergo multiple acceptance tests including thermal, vibration and final performance testing.
The company continuously improves its processes and products, pinpointing chances to streamline work and ensure product quality, including for instance highly accurate 3D maps of its emitters early in manufacturing, allowing to predict performance later.

Sustainable and Dependable Relationships
The focus of ENPULSION’s efforts is to further advance its position as the most dependable tier-1 in-space mobility solutions supplier in the market. This includes providing the most efficient and reliable electric propulsion systems, putting to the greatest effect its industrial capabilities as well as offering short and reliable lead times, and building long-term, sustainable and dependable business relationships with partners, satellite manufacturers and operators. Thus enabling the sustainable use of orbital resources and innovative business models for a thriving near-earth economy.